The Cutting Die For Cam Blister Machines With Positive Logic Rejection
Main benefits and characteristics of the cutting die for CAM blister machines with positive logic rejection, called SLP
GOOD BLISTERS ONLY
The new cutting die designed by Partena, the CAM manufacturer specialising in the design and construction of blister machines, deposits only compliant blisters on the outgoing belt; any rejections, incomplete and empty blisters are expelled before the machine outfeed belt, with the optional possibility of separating the waste into different containers.
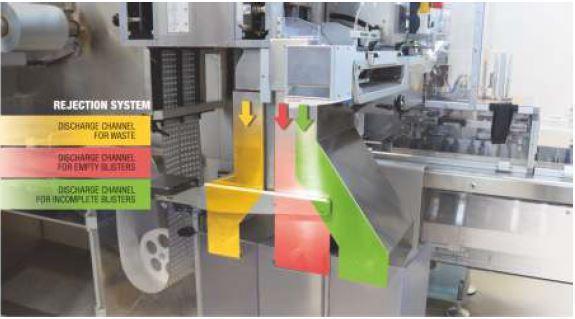
Furthermore, the new cutting die device has been studied and designed with the intention of guaranteeing:
- Product quality
- Easy and quick format changeover
- Proper and reliable operation
- Automatic compensation of machine speed variations
- Standardization and reduction of the types of components
- Optimization of the primary area
- Maximum flexibility for maximum efficiency
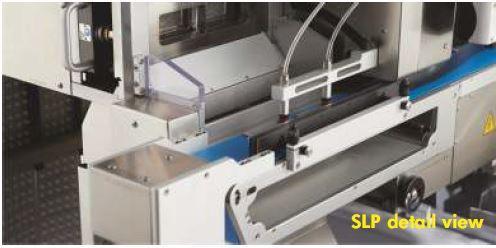
Product Quality
The precision of the cutting position is guaranteed by sensors placed before the cut that read the position of the cavities with precision; also thanks to the constant reading of the blisters the system is able to detect any systematic errors of position, correcting them and showing on the operator panel the graphical trend of the detected errors.
The quality of the blister is also guaranteed in the event of stoppage; in fact, when the machine stops, the blisters in the yielding roller would risk remaining for an excessively long period in a curved position, with consequent deformation that could be problematic for the machine feeder downstream and in any case with the risk of causing discontinuity with respect to the other blisters that have been processed correctly.
For this reason, in the event of stoppage, the tension on the belt is removed to avoid excessive bending of the blisters.
Easy and Quick Format Changeover
CAM has designed and developed the cutting die seeking to limit the format parts. For example, created with the same cutter, they share the same rotary gripper and the same guides, and for standard size blisters the SLP outfeed belt has an adjustable position. In this manner it can be adapted without the need to construct format parts.
Furthermore SLP is equipped with a system that reads the position of the thermoformed tape. Upon format changeover, all that is needed is to pass a stroke under the reading system that will recognise the blisters and their position and will automatically set the position of the cut, without the need for any manual adjustment.
Finally all the parameters can be programmed from the operator panel or by graduated systems that guarantee a high level of ease and repeatability of format changeover, so that it can be performed by any operator. For example, the barrier photocell that records the rejection can be programmed directly from the operator panel by entering the format of the stroke without having to perform any manual adjustment.
Proper and Reliable Operation
A system to control the torque required on the cutting motor shaft guarantees correct operation of the unit: if the torque is outside the determined range, the system warns the operator and immediately stops the machine.
Automatic compensation of machine speed variations
SLP is independently motor-driven, so its connection to the other stations of the machine does not feature a fixed ratio: SLP automatically adjusts its speed and consequently slows down or accelerates, depending on the progress of the stations upstream. Moreover, thanks to the separation of the mechanical cutting cycle from that of the thermoforming machine, the cutting die can be stopped immediately, without having to complete the cuts of the stroke, with consequent release of the relative blisters on the belt.
Standardization and reduction of the types of components
The logic of the rejection system is managed by the PLC rather than by the vision system, potentially allowing interfacing with a greater number of vision system suppliers.
Optimization of the primary area
The SLP is both available in the integrated version within the blister packer basement and in the standalone version. The stand-alone version is particularly interesting for those production solutions requiring the separation between the primary and secondary phases by means of a cleanroom. In fact, the standalone version of the cutter permits to keep the only phases necessary to pack the product in blisters on the controlled atmosphere blister packer, and sends a continuous belt of blisters to the secondary area with the product already sealed.
The blister machine without blister cutting reduces its length by about one meter. The result is a cleanroom with optimized dimensions, hence a reduction in production and management costs, as well as a simpler handling of the product leaving the cleanroom itself.
Maximum flexibility for maximum efficiency
Only compliant blisters can leave the blister packer, and this permits to easily arrange a blister recovery system if the cartoner stops. In fact, should the cartoner stop for any reason, the SLP would automatically reverse the running direction of the outfeed conveyor belt in order to recover the blisters on a temporary storage system; the blisters thus recovered can be inserted again in the packaging cycle, so that to grant the maximum line efficiency. This operation mode will be even more important if the line has also to produce small lots.
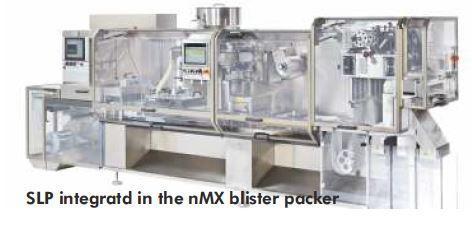